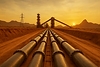
The Best Slurry Lining Solutions for your System

Choosing the right slurry lining depends on several factors, including the type of slurry being transported, the operating conditions, and the specific requirements of your system. Whether you’re dealing with abrasive, corrosive, high-pressure and high-temperature conditions, our engineer consultants will help evaluate all factors to determine the best solution for your needs.
The Right Choice of Slurry Lining
The right choice of slurry lining will depend on your specific operational conditions, the nature of the slurry, and your budget. Abrasion resistance, chemical resistance, pipe diameter, pressure, temperature tolerance, cost and durability are all factors to consider. Our engineer consultants can determine the best solution for your specific needs.
Natural Rubber/Gum Rubber (40 to 60 Shore D):
Industry standard due to its low cost and ease of installation. It offers high tear and great abrasion resistance characteristics, the vulcanizing curing process creates a superior metal to rubber bond. It is installed in hand laid sheets and plied up to the desired thickness. This material is not ideal for outdoor (UV), hydrocarbon or acidic environments. Typical applications include slurry pipes, sumps, trommels, and flotation cells.
-
40D – optimal for fine particle slurry applications
-
60D – optimal for larger or sharper particles higher velocity
Neoprene (60 Shore D):
A synthetic rubber with strong tear and good abrasion resistance while maintaining strong resistant to UV rays. It is ideal for some chemical environments. Neoprene is bonded to metal by a vulcanizing curing process. Installed in hand laid sheets up to the desired thickness. Typical applications are slurry pipe, sumps and launders where outdoors or chemical resistance is required.
Nitrile (60 Shore D):
A synthetic rubber with lower abrasion characteristics than Natural Rubber. Nitrile also bonds well to metal during the vulcanizing curing process. Installed in hand laid sheets up to the desired thickness. Ideal if some chemicals, gas, or oil are present. Therefore, it is a great alternative for Natural Rubber. Typical applications are slurry pipe, sumps and trommels where a lining with superior chemical resistance is required.
BPC (35 Shore D):
Superior grade rubber exhibits great abrasion properties, while maintaining all benefits of Natural Rubber. BPC is bonded to metal the vulcanizing curing process. Installed in hand laid sheets up to the desired thickness. It is ideal in the highest wear applications, associated with increased velocity and/or impact.
Polyurethane (80 to 95 Shore A):
An elastomeric product similar to rubber with lower friction properties along with great abrasion properties. It exhibits a stronger resistance to damage caused by UV rays, and additives can be used to increase that resistance. Cold bond methods are used to create a strong metal to urethane bond. It can be applied by casting or spray methods. It performs well in chemical applications (pH 2-12) and hydrocarbon environments. It is ideal for lower slurry velocity or irregular shaped environments. The sprayed application allows for varying thickness to accommodate unique wear patterns and complicated parts.
-
80A – Higher velocity slurry environments
-
95A – Strong release properties
Ceramic:
A hard Alumina Ceramic material with excellent abrasion properties for harsh/ high wear conditions. It is ideal in environments with corrosive material, and extreme temperatures. It can be bonded to a steel backing using epoxy, urethane or rubber. It is not ideal in extreme impact conditions. Applications slurry pipes, slide chutes, and transitions where no tramp metals are present.
Silica Carbide:
A hard crystalline compound made of silicon and carbon. It exhibits exceptional wear resistance and hardness in extreme abrasion environments where no tramp metals are present. It is also known as Black Ceramic. It can be bonded to a steel backing using epoxy, urethane or rubber. Typical applications are fine particle transfer points in cyclone vortex finders and tub walls.